Vibration monitoring has a long history and has been used as a fault detection and diagnosis technique for rotating machines for more than 60 year. The traditional methods for vibration monitoring are either data collection by portable analyzers or real-time monitoring using wired on-line systems. The latter consists of installing vibration sensors on rotating machines and connecting them to the monitoring system through a long path of cabling. The traditional on-line vibration monitoring systems are usually very expensive and they are only cost-effective for critical machinery that may fail in a short period of time. On the other side, portable vibration data-collectors are used to record vibration on a monthly basis which is not enough for many of the rotating machines which are not also reasonable choices for on-line monitoring. Newly developed wireless vibration sensors can bridge the gaps between these two traditional solutions for vibration monitoring. P-CUBE is an example of wireless vibration sensors. They are very cost-effective and easy-to-use tools and do not need any cabling as they send the data to the cloud servers through Wi-Fi. The simplicity of use and cost-effectiveness of wireless vibration sensors allow the users to install them on hundreds of rotating machines. This way, it is possible to measure and trend the machines’ vibration several times a day. This will improve the effectiveness of the condition monitoring program considerably as it makes it possible to detect the faults earlier.
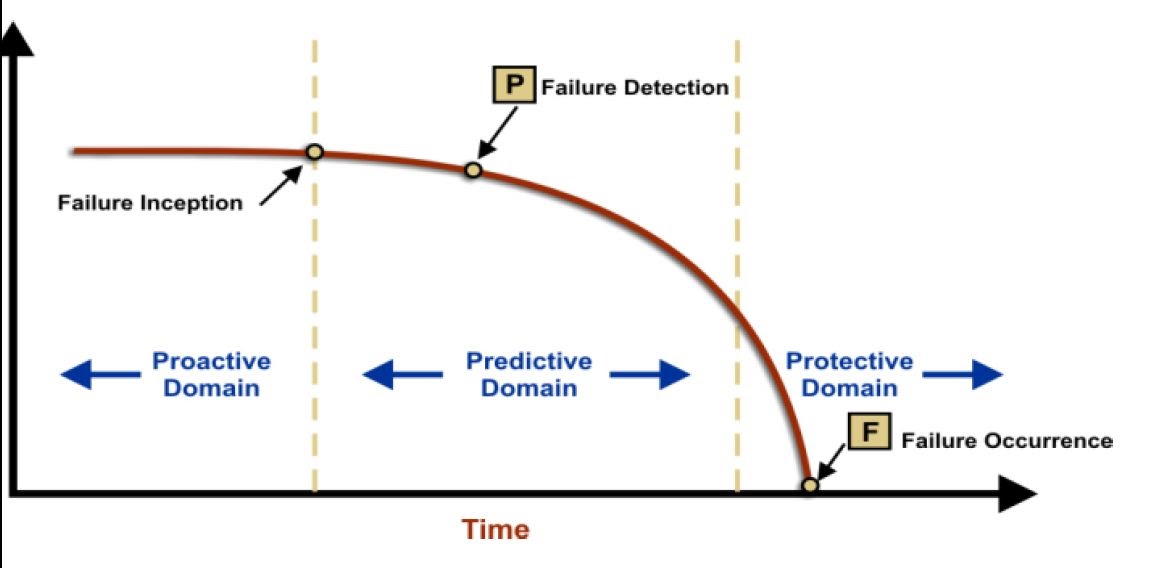
Furthermore, the wireless vibration sensors are very effective in monitoring the rotating machines in remote locations and where there are some hazardous situations making it difficult for a human to get access. There are numerous examples of machines that cannot justify the use of traditional wired on-line monitoring systems and cannot be added to the off-line measurement program because of their location and safety issues. The wireless sensor is the best choice for these cases.
Using wireless sensors for vibration monitoring makes it possible to measure the vibration every few hours. This helps to identify a deviation and intervene before the occurrence of a failure with enough lead time for planning the required action. It also provides an opportunity to evaluate the vibration trends along with the process conditions that is very crucial for finding the root cause of the problems for turbomachines.
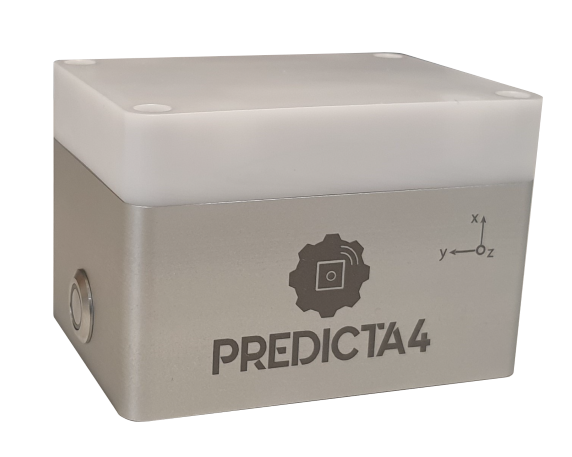
They are a complementary solution to cable-based on-line systems and portable vibration measurement systems and make it possible to monitor more equipment in order to improve predictive maintenance performance. They are less expensive and prove to be profitable with respect to equipment value, cost of spare parts or fewer downtimes. So, it is necessary to integrate this new generation of vibration monitoring into the predictive maintenance strategy.
Leave A Comment
You must be logged in to post a comment.